Rawlings
REV1X MLB glove
Client
Rawlings
Year
2021
Website
rawlings.com/REV1X
Services
Product Design (3D)
Product Development
Product Strategy
Mechanical Engineering
Prototyping
Additive Manufacturing
Design for Manufacturing
Design for Assembly
Validation & Testing
Pilot Production
Vendor Liaison
Production Ramp Support
An ultra-lightweight, form-fitting game-ready MLB glove that gives you consistently unmatched playability across the field.
During my time at Carbon, I had the pleasure of visiting the Rawlings Leather Lab in St. Louis, Missouri to kick off a design sprint workshop to explore how we could improve player performance and revolutionize baseball gloves with 3D printing. With a clear vision and product requirements in place, I had the opportunity to lead the design behind these components of the glove with Rawlings while working closely with Robert Newman, Marc Schmidt, Mitchell Hinrichsen, Ryan Farrar, and some of the experts at Rawlings. After several iterations, testing, and player feedback, we successfully got this breakthrough product into production with Fast Radius, on players’ hands all across the MLB, and now they have finally hit the market!
I owned the product design and development of the internal latticed finger support - computationally designed in nTopology and additively manufactured with Carbon DLS. An optimized lattice structure in the pinky & thumb material of the glove allows for variable stiffness, significantly light weighting the glove without sacrificing protection or durability.
Learn more about the story at www.carbon3d.com/rawlings and get the REV1X now for $399 at Rawlings.com, JustBallgloves.com and DicksSportingGoods.com.

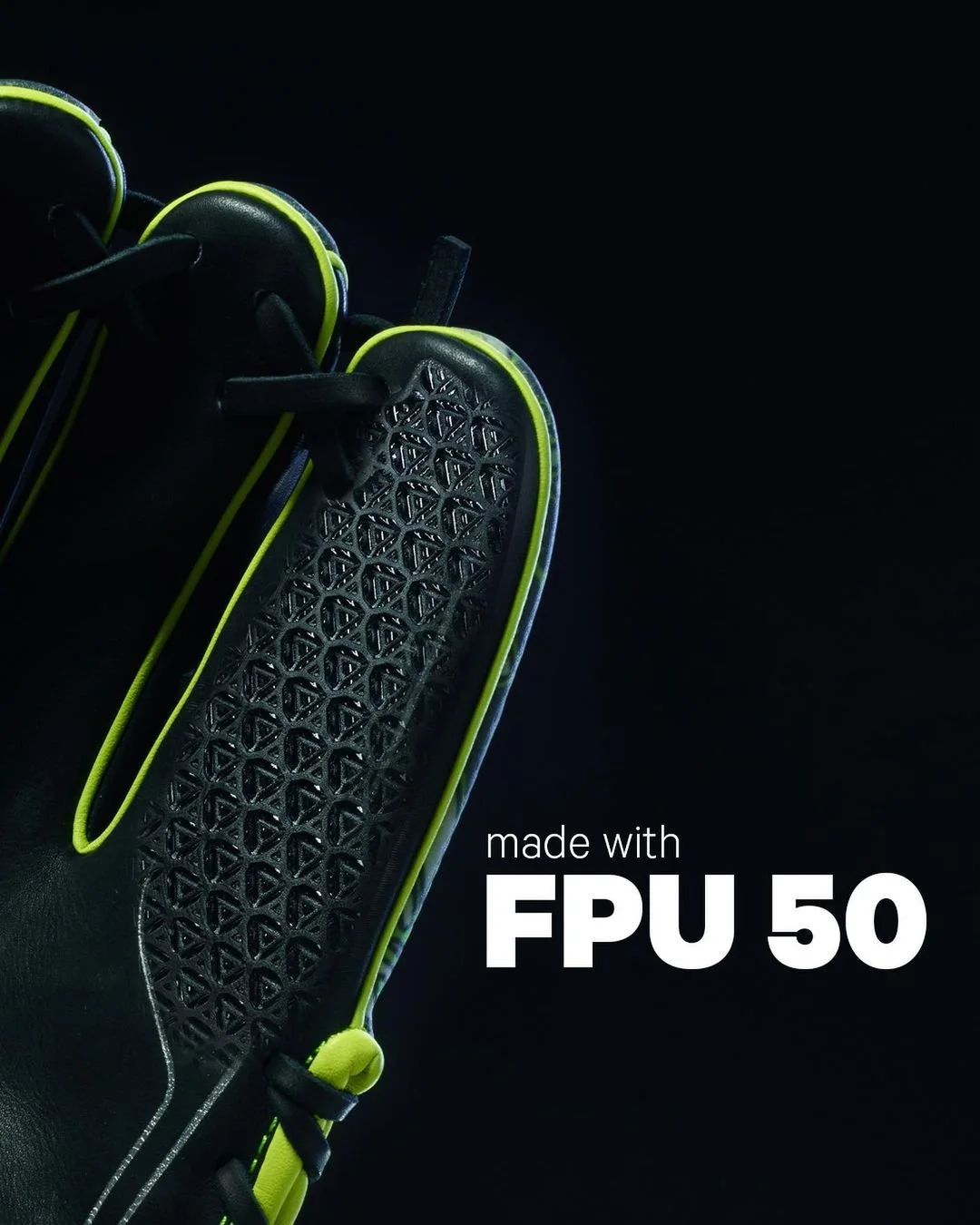
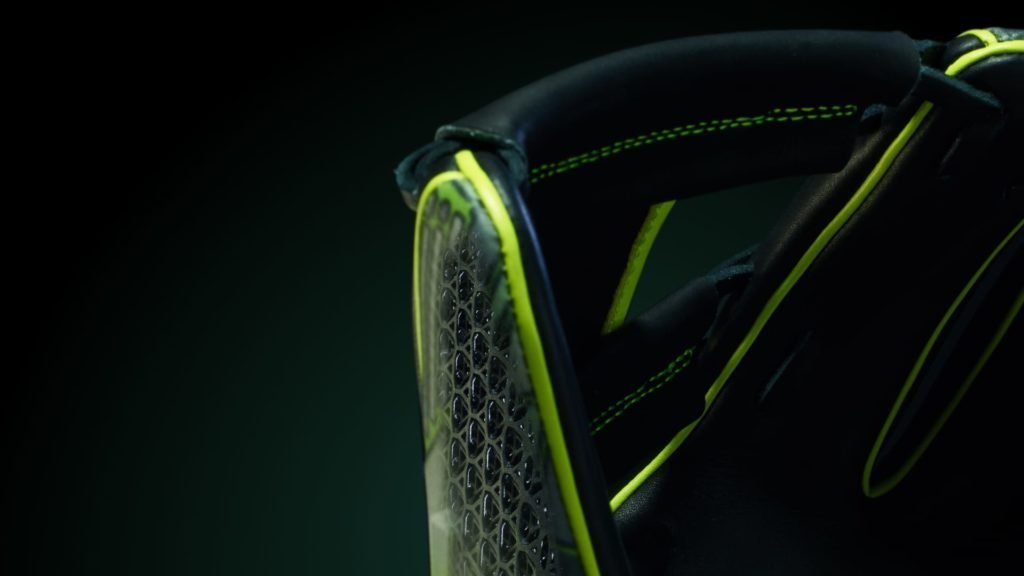
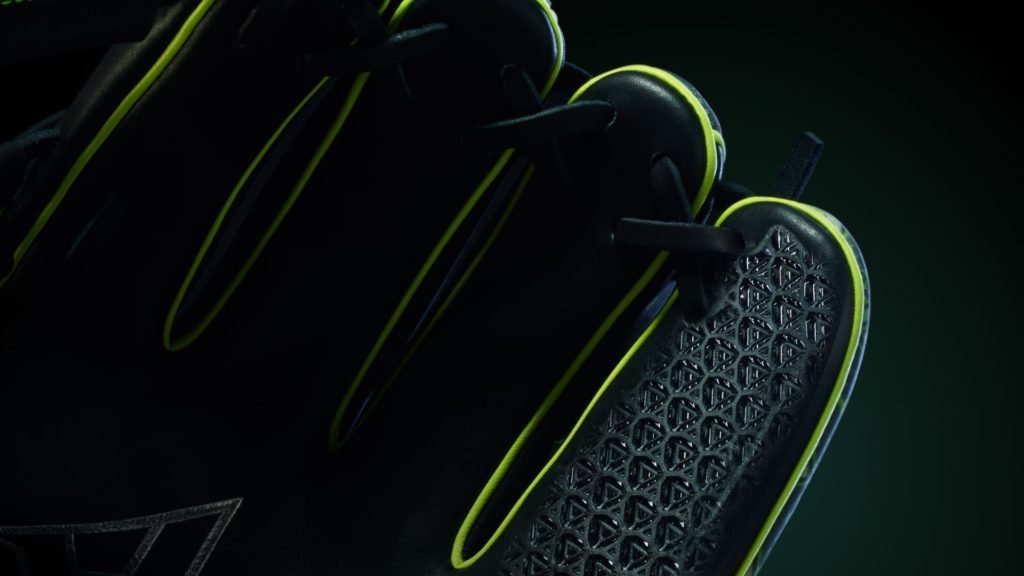




Prompt
How might we create an MLB glove to improve player performance?
Challenge
Baseball is rooted in tradition. Players are passionate about their equipment almost as much as they are about the game. While they are skeptical to new gear, they always seek ways to improve.
How do we design a glove that is lightweight to enable faster reaction times for fielders?
How do we choose materials that reduce time to break in to be game-ready sooner, and last longer in its ideal form?
How do we use structures to control stiffness and ensure the ideal glove configuration: stiff thumb, stiff pinky, and soft pocket ?
Solution
Process
I guide my client through a phase gated 6 STEP PROCESS from definition to delivery:
1: Exploration
Exploration consists of 4 stages: Select, Specify, Validate, and Assess.
Select
Every project begins with identifying the client’s objectives and understanding their vision, to select strong application candidates.
We do a product teardown to learn about how the these gloves are assembled and to evaluate the felt material used:
During these meetings, I gather product requirements and qualification plans in order to evaluate feasibility.
Here are some critical considerations:
Specify
We brainstorm concepts based on our preliminary requirements. I do this by moderating in-person design sprints with key stakeholders to unpack insights for player needs, document how it influences design, create plans for testing, and refine product strategy. I also ask questions about other aspects of the glove that these parts will integrate with. The client chose a PU outer liner to further lightweight the glove while maintaining a traditional leather liner on the ball contact surface. We evaluate the risks of each option and how it affects the overall assembly of the glove.
Some notes from our white-boarding and early sketches:
In collaborating with the client’s industrial designer, we conceptualize the product vision together.
In this stage, I also educate the client on how to design for DLS™. This enables them to collaborate with us to utilize Carbon’s technology for product development.
I walk the client through best practices for DfAM such as these:
Design
At this point, the product architecture is defined and materials selection is complete.
The CAD (Computer Aided Design) and AAD (Algorithmic Aided Design) work begins.
Each finger has unique requirements. I go through multiple iterations to revise the design of the structure. I make changes to both the form of the finger inserts and the lattice within it, to fit the client’s expected performance requirements, all while ensuring it can be manufactured and assembled.
Prototyping
Soft Pocket (EPU 40)
Stiff Thumb (FPU 50)
Stiff Pinky (FPU 50)
Validation
The client defines their own testing methods to evaluate flexure and the effects of cyclic loading by measuring reaction forces. We also measure critical dimensions and the mass of each part. The testing conditions included ASTM G154 for 100 hours but with no direct UV exposure. There were a total of 1000 cycles in fatigue as well.
Together we analyze the test data and use that as insight to revise the design, in an iterative process.
Test Method 1: Flexural testing
Test Method 2: Fatigue test
We measure the mass in grams on a scale for the Carbon parts as well as the conventional felt equivalent and track this throughout. . We also measure critical dimensions using a CT scanner check to ensure we are within an allowable tolerance.
Test Method 3: Metrology
Assess
The final design we arrive at was tested and indicates that the new glove has a 30% reduction in weight and more than doubles the stiffness-to-weight ratio of the client’s premium product. This means that the client can now provide baseball players with the ideal flexural properties desired in a glove by simply engineering the DLS-printed latticed finger inserts.
Furthermore, the glove starts off closer to “broken-in”. It holds up longer over multiple loading cycles, as evident in the smaller percentage delta in the EPU and FPU glove inserts, as opposed to the client’s felt inserts.
2: Alpha
Now that we’ve proven technical feasibility for a functional prototype, we deliver production samples and confirm DLS can deliver all the production requirements necessary to begin scale-up efforts.
At this point, commercialization discussions are underway. I help guide the client towards decision-making through a robust cost analysis by modelling production volumes, material, waste, labor, utilization, etc, to determine part economics.
Our next steps are to continue refining other aspects of the glove that integrate with these inserts, in order to move towards a design lock for validation.
Here is an overview of the various glove components and materials, designed locked for validation:
3: Beta
At this point, production solutions such as baking fixtures are explored to limit warping during the curing stage and to ensure satisfactory quality control during visual inspection.
Subsequently, this was deemed irrelevant since the parts would not be visual once installed into the gloves. We abandoned this baking fixture pictured below.
Production builds are optimized and fine tuned for maximum throughput, while assuring quality and consistency.
Here, we analyze yield from each production build and work on making the necessary revisions to improve yield.
The client measures quality by metrology studies for shrinkage that will prevent proper assembly and integration.
4: Pilot
At this stage, I pull in folks at Carbon to assist in coordinating with the client’s marketing team to enable the client to clearly communicate the value add with DLS and the new components in the glove, while ensuring it is on brand.
Sales samples of the glove are prepared alongside the client’s product packaging, ready for their sales reps to take to MLB pro players, in order to gather interest and feedback.
The gloves go through design validation during spring training season and any revisions are made thereafter.
5: Production Transfer
At this stage, we let the client decide if they want to go with the OEM (Original Equipment Manufacturer) route of onboarding printers themselves or if they would like to be connected to a CM (contract manufacturer). The client decided to go with a CM, so we helped facilitate that transfer.
6: Production
The CM is now collaborating directly with the client as they go to market with this product.